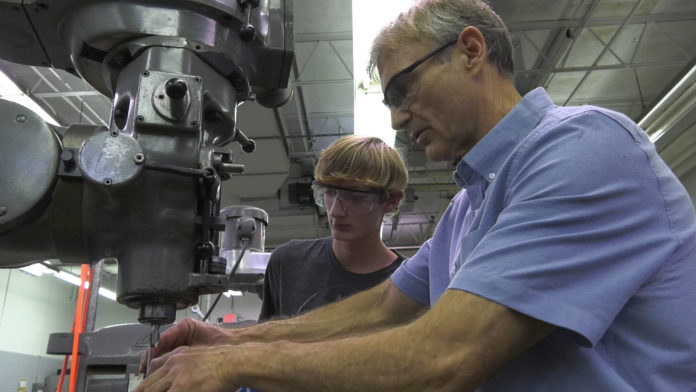
NASA now has a few high school students who will be a part of a major program. Students at an Alabama high school are now making parts for use on the International Space Station.
NASA has been sponsoring programs to build the spark in students in the field of aerospace industry for more than 50 years. One of them is HUNCH (High Schools United with NASA to Create Hardware). This challenges students to use machining, welding and other skills learned in class to build exact prototypes of the hardware on the space station. Astronauts and flight controllers use these mock-ups for ground training before a mission.
HUNCH has been a part of the curriculum at Austin High School in Decatur, Alabama, since 2010. Bill Gibson is the school’s Machine Tool Technology instructor and a fierce advocate for this kind of hands-on training.

Credits: NASA
Bob Zeek, HUNCH co-founder and program manager, said, “We realized early in the station program that we needed a version on the ground before we flew in to space”. “At the same time, we wanted to get kids who are good at machining, welding, or other technical skills involved with NASA”.
This year, the challenge was to build two items. One is a set of bolts that will hold lockers of scientific experiments. And the other is a holder for a new brush cleaning tool for use during spacewalks. The tenth SpaceX cargo resupply mission which launched Feb. 19 delivered the tools to the space station.

Credits: NASA
Ryan Anthony, a senior at Austin High School shared his experiences. He said, “I was nervous when I found out we would use hardened stainless steel. That’s when I knew this would be completely different learning experience for all of us”. He also feels proud about the student made tools which will find its place in space station.
HUNCH shows students the real-world application for the machining they perform in class. The next-level experience not only includes manufacturing unique pieces of hardware, but also learning to use new high-tech tools. It also includes creating computer-aided design drawings, and dealing with extreme precision.
The small pieces students make are big steps in training the workforce. This will help design and build the space-faring vehicles of tomorrow.